Next Generation Engineering (NGE) chains and belts are IRP Engineering Plastics Powered By SystemFlex’s newly engineered resins designed to provide a sustainable advantage over “industry standard” materials. NGE’s reduced coefficient of friction properties enable end users to reduce or eliminate their chain/belt lubrication, thus providing a true “dry running” conveyor.
These dry running applications also result in reduced power consumption, increased wear life, reduced dust generation and the ability to run at higher speeds.
IRP Engineering Plastics Powered by SystemFlex and NGE
We are leading the way with local manufacturing by providing exciting new products and developments like that of our Next Generation Engineering Material (NGE). Recognizing the opportunity to locally manufacture NGE products that offer new possibilities for running conveyor lines without lubrication. This enabled the reduction/elimination of soap & water or dry lubricants, creating a safer work environment and cost savings. NG material has also proven it provide longer wear life in comparison to acetal materials and reduces noise levels in dry applications.
What are the benefits of NGE?
NGE offers lower friction, reducing resistance and improving efficiency. It also leads to decreased water and lubrication costs, saving on resources and expenses. Additionally, NGE provides higher strength and improved abrasion resistance, enhancing durability and performance. It is approved for direct food contact according to EU and FDA regulations, ensuring safety and compliance. Furthermore, NGE contributes to noise reduction, creating a quieter operating environment.
Dry Running NGE – What are running applications?
In industrial settings, dry running refers to machines and systems that operate without using traditional lubricants like oil or grease. This might sound like a risky move, especially when we’re used to thinking of lubrication as essential for smooth machine operation. But guess what? Dry running applications are not only possible—they’re becoming increasingly popular for their efficiency, low maintenance, and environmental benefits.
In this article, we’ll break down what dry-running applications are, explore their advantages, and dive into the industries that benefit from them. Ready to learn how machinery can run smoothly without a drop of oil? Let’s get into it!
What are Dry Running Applications?
Dry-running applications refer to mechanical systems or equipment that operate without lubrication. In traditional systems, lubricants like oil or grease reduce friction and wear. However, dry-running applications are designed to run smoothly without the need for these substances, thanks to advanced materials and designs that minimize friction.
In these setups, components such as bearings, seals, and belts are typically made from self-lubricating materials or engineered plastics that can withstand the stresses of operation without the need for additional lubricants. This makes dry-running systems ideal for situations where using traditional lubrication might be impractical, undesirable, or environmentally harmful.
How Do Dry Running Applications Work?
The secret behind dry-running applications lies in the materials and technology that minimize friction and wear. These systems often rely on the following:
Self-Lubricating Materials: Many dry-running components are made from engineered plastics, ceramic composites, or advanced polymers. These materials have inherent properties that reduce friction, even under continuous operation.
Specialized Designs: Components such as seals and bearings are designed precisely to ensure minimal contact friction. This helps reduce the wear and tear typically associated with machines that operate without lubrication.
Heat Dissipation: In dry running systems, controlling heat is crucial since no lubricating fluid can cool components. These systems are often engineered to dissipate heat efficiently, preventing overheating during operation.
Advantages of Dry Running Applications
Dry running applications have many benefits, especially for industries looking to improve efficiency, reduce costs, and minimize environmental impact. Let’s take a look at the key advantages:
- Reduced Maintenance: Dry-running systems require less frequent maintenance without the need for lubricants. This reduces operational downtime and the costs associated with regular lubrication schedules, such as oil changes or grease applications.
- Cleaner Operation: Since no lubricants are used, there’s no risk of oil spills or working environment contamination. This makes dry running ideal for industries where cleanliness is a priority, like food processing or pharmaceuticals.
- Environmentally Friendly: Traditional lubricants often contain chemicals that can be harmful to the environment. By eliminating the need for these substances, dry-running applications help reduce the environmental impact of industrial operations. Additionally, there’s no need to dispose of used oils, which can pose a significant ecological challenge.
- Cost Efficiency: Over time, the costs of purchasing, applying, and disposing of lubricants can increase. Dry-running systems eliminate these expenses, leading to long-term cost savings.
- Improved Machine Life: Dry-running components are often designed to be highly durable and resistant to wear. This increases the equipment’s overall lifespan and reduces the need for frequent part replacements.
- Fewer Contamination Risks: In sensitive industries like food and beverage production or pharmaceuticals, lubricant contamination can pose serious risks. Dry-running systems eliminate this risk, as lubricants cannot leak into the product stream.
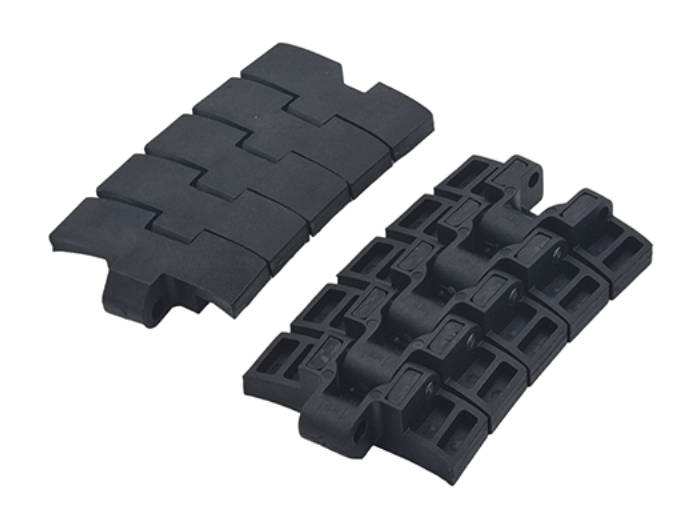
Applications of Dry Running Technology
Dry running technology is used in various industries, particularly in environments where cleanliness, safety, and reduced maintenance are paramount. Here are some of the most common applications:
- Food and Beverage Industry: Dry-running applications are preferred in food production because they minimize the risk of contaminating food products with lubricants. Conveyors, packaging machines, and bottling systems often use dry-running components to maintain strict hygiene standards.
- Pharmaceutical Manufacturing: Just like in food production, pharmaceutical manufacturing requires an ultra-clean environment. Dry running systems help ensure that no lubricants come into contact with sensitive medicines or packaging.
- Textile Industry: Textile machines operate at high speeds, and lubricant contamination can ruin fabrics. Dry running technology provides a clean, efficient solution for high-speed looms and other textile machinery.
- Water Treatment Plants: In water treatment, machinery often operates in a wet environment where traditional lubrication would wash away. Dry running systems, especially those made from corrosion-resistant materials, are perfect for this setting.
- Packaging and Bottling: Dry running conveyors are commonly used in the packaging and bottling industries, where spillage from lubricants could damage products or packaging materials. The clean operation of dry running systems makes them ideal for handling delicate items.
How to Implement Dry Running Systems
Thinking about implementing dry running systems in your industrial setup? Here are a few things to consider:
- Material Selection: Choose the right self-lubricating materials for your equipment. Engineered plastics and advanced polymers are excellent options for minimizing friction and wear in dry running applications.
- Component Design: Ensure that your components—like bearings, seals, and belts—are designed specifically for dry running conditions. This includes looking for precision-engineered parts that reduce contact friction and efficiently manage heat dissipation.
- Temperature and Load Limits: Pay attention to the operational limits of your dry running components. While these systems are designed for durability, they may have specific temperature or load capacity requirements to ensure long-term efficiency.
- Consult Experts: If you’re new to dry-running technology, consult with IRP’s industry experts. We can guide you on the best materials and components for your particular application.
FAQs
- Is dry running safe for all industries?
While dry-running technology suits many industries, certain applications—like those with extreme heat or high-pressure environments—may still require lubrication to prevent overheating or component failure. - Can dry-running systems handle heavy loads?
Yes, many dry-running systems are designed to handle heavy loads, provided they are made from high-strength materials like engineered plastics or ceramic composites. - Are dry-running systems more expensive to install?
While the initial cost of dry-running components might be higher than that of traditional systems, the long-term savings in maintenance, lubricant costs, and downtime usually offset the upfront investment. - Do dry-running systems require any lubrication at all?
No, dry-running systems are specifically designed to operate without lubrication. They use self-lubricating materials and precision-engineered designs to minimize friction and wear.
Dry running applications are revolutionizing industries by offering a cleaner, more efficient, and environmentally friendly way to keep machines running smoothly. From food processing to pharmaceuticals and packaging, dry-running systems provide innovative solutions to common industrial challenges—without the need for traditional lubricants.
By embracing dry-running technology, industries can reduce costs, improve operational efficiency, and positively impact the environment. Whether you’re looking to minimise contamination risks, reduce maintenance, or find a more sustainable solution for your machinery, dry-running applications could be the answer.